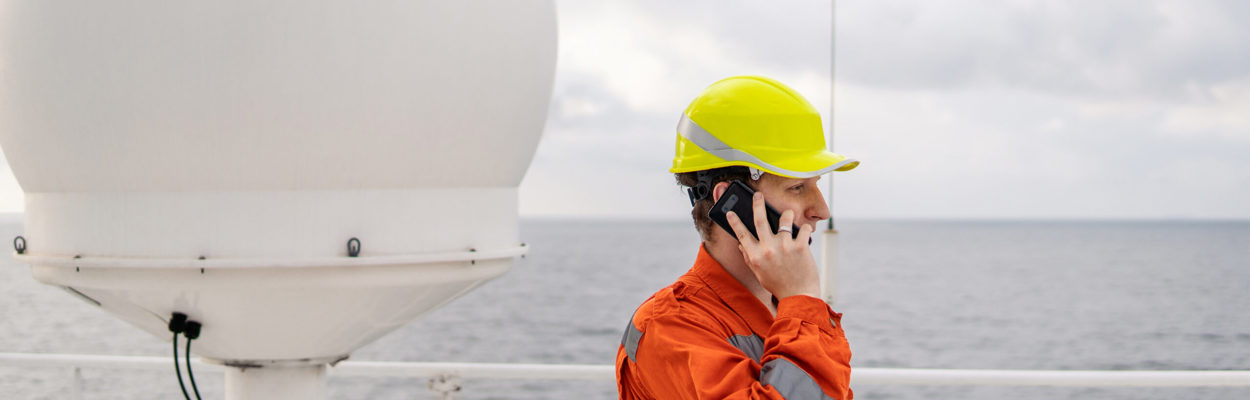
Save time and money:Maritime Predictive Maintenance
To survive and thrive through challenging times needs proactive leadership rather than reactive. In the shipping business, waiting for something to go wrong before you try and fix it risks putting strain on other components, as well as waste fuel, lose time, miss opportunities and risk safety.
The standard model of maintenance has – for years – been based on the known mean time between failures (MTBF) of components. Operators have approached maintenance as a time-based, preventative programme. The US Navy concluded in a 1982 study that even with the best engineers working diligently to a perfect routine of inspection and servicing, less than a quarter of machine failures would be caught before it was too late. Around 77%, concluded the US Navy, were random.
Maritime predictive maintenance and condition monitoring
Fortunately, there is an answer, condition monitoring (CM). CM is an automated process of continual machine inspection, an early warning system of mechanical problems. Although over three-quarters of mechanical failures are random, machinery doesn’t just break without warning. Continual monitoring reveals patterns of temperature, pressure and vibration data that can predict when maintenance is needed.
When condition monitoring runs continually, data can be collected and delivered to shore where powerful diagnosis and analysis programs can be run, tailored to each piece of equipment. Until recently, moving data from ship to shore was often prohibitively expensive, but Telenor Maritime’s high frequency mesh radio network was designed to handle this task efficiently and affordably.
According to Juho Jaakola, the Head of Maritime System Sales at Telenor Maritime, there are many benefits. “Now that Telenor Maritime’s mesh radio system makes secure connectivity between vessels and the shore affordable and scalable, predictive maintenance becomes possible. If errors are noticed in a particular system during a voyage, not only does the vessel owner have an early warning and can prevent further problems, but spare parts could be delivered to the next port ready for installation, saving time at the dock.”
In a competitive industry that always has one eye on the bottom line, condition monitoring and predictive maintenance make sense. Now that affordable and scalable connections to shoreside systems are available, there’s a very bright future ahead for the industry if predictions are anything to go by.
Condition monitoring and predictive maintenance can improve efficiency and lead towards a greener, more sustainable future. Find out more and book a live demonstration by mailing maa@telenormaritime.com